Key Takeaways
- Tanker trucks are built to transport specific materials like fuel, chemicals, food, and gases using regulated tank designs.
- Each tanker type has defined volume capacities based on cargo safety, road weight limits, and tank construction.
- Federal regulations control driver certification, tank specifications, and safety systems to prevent leaks and accidents.
- Matrack improves tanker logistics by offering GPS tracking, ELD compliance, safety monitoring, and fuel cost control.
What Is a Tanker Truck?
A tanker truck is a transport vehicle designed with an integrated tank to carry large volumes of liquids or gases. It handles substances such as fuels, edible liquids, chemical compounds, and cryogenic materials.
The cylindrical tank structure maximizes pressure containment and increases transport volume. This shape improves cargo stability and reduces internal surge during motion.
Tanker trucks reduce logistics dependency on fixed terminals by enabling direct source-to-destination delivery. These structural and operational differences define the types of tanker trucks used across specialized industries.
What Are the Types of Tanker Trucks?
There are 6 types of tanker trucks, each designed for a specific category of bulk cargo.
1. Fuel Tanker Trucks
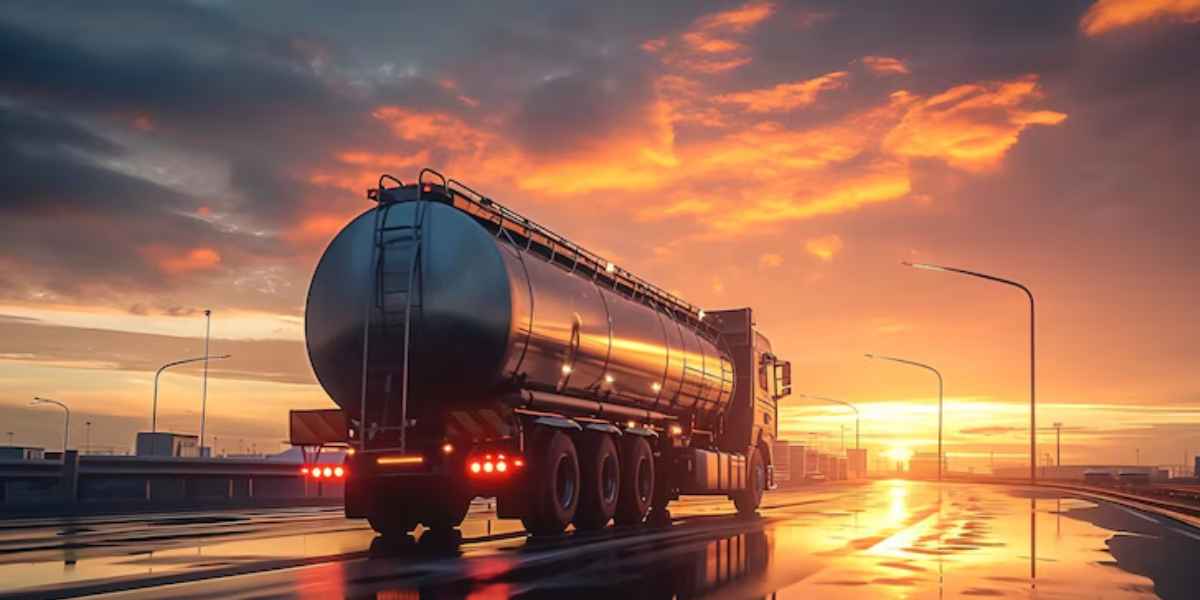
Fuel tanker trucks are designed to transport flammable liquids like gasoline, diesel, or aviation fuel. These tankers primarily use DOT-406 specifications, with low-pressure aluminum or carbon steel tanks and top-loading configurations.
To prevent vapor loss and control pressure, they use vapor recovery systems and emergency shut-off valves. Fuel tankers often feature multiple compartments to separate fuel grades during distribution.
2. Chemical Cargo Tank Trucks
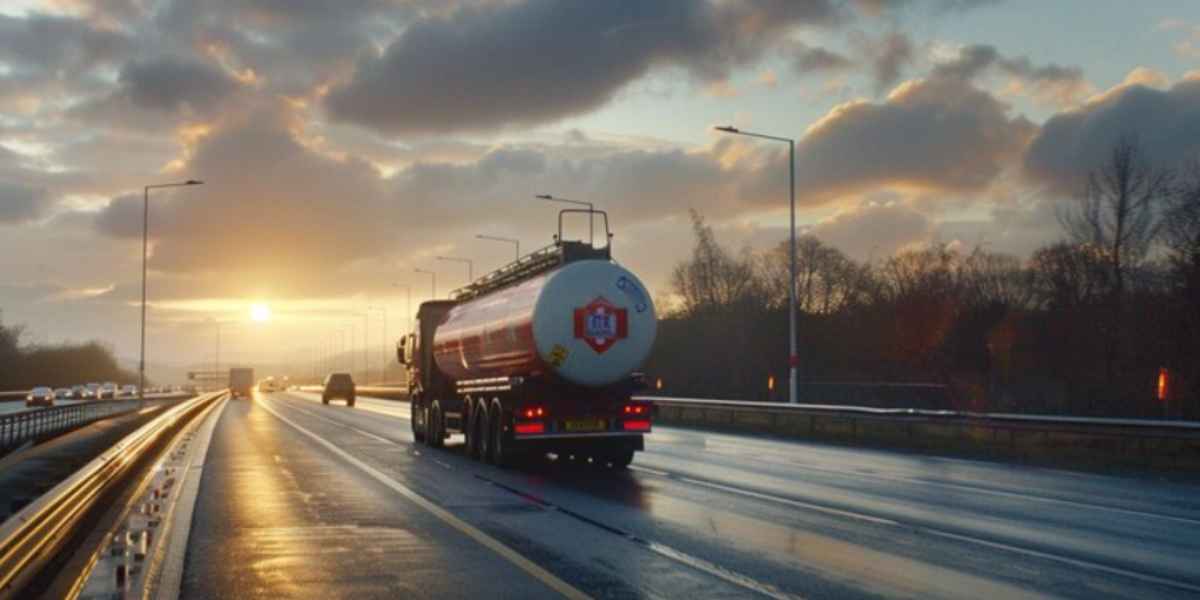
Chemical tankers move hazardous materials such as acids, solvents, or industrial reagents. These tankers are often built under DOT-407 or MC-307 standards, allowing moderate pressure containment with corrosion-resistant linings.
Tank interiors use rubber, fiberglass-reinforced plastic, or specialized resins depending on the chemical profile. External piping and sealed manholes reduce exposure risks during loading and unloading.
3. Food-Grade Cargo Tank Trucks
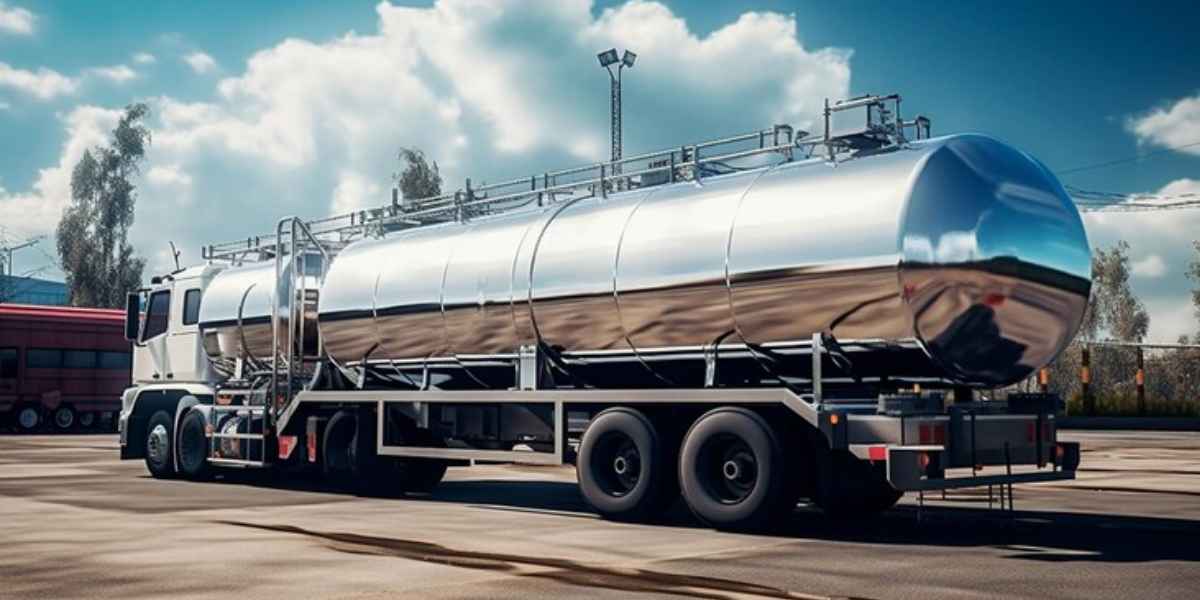
Food-grade tankers are used for transporting liquid food products like milk, vegetable oil, or corn syrup. These tankers follow sanitary transport guidelines and are constructed with high-polish stainless steel interiors to prevent bacterial buildup.
They use CIP (Clean-in-Place) systems, temperature retention jackets, and sterile fittings to preserve product integrity. Food-grade tank trucks do not allow mixing of different cargo types to avoid cross-contamination.
4. Cryogenic Cargo Tank Trucks
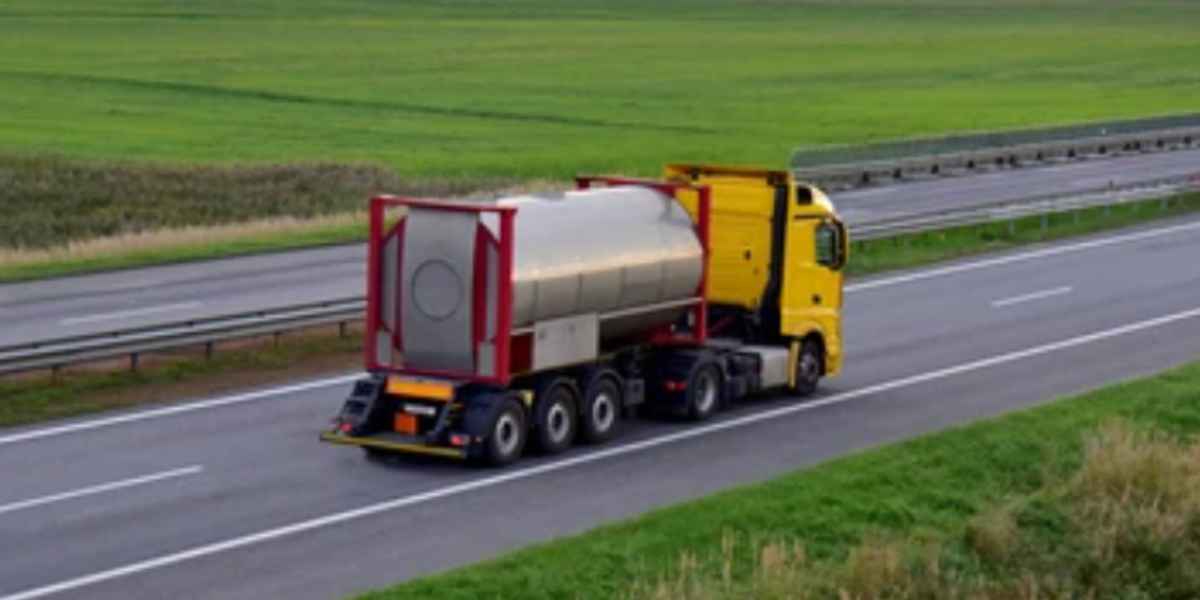
Cryogenic tankers are engineered to carry liquefied gases such as nitrogen, argon, or oxygen at temperatures below -150°C. These are regulated under MC-338 or TC-338 codes, which require double-walled construction and vacuum-sealed insulation.
The outer shell supports structural integrity, while the inner tank maintains ultra-low temperatures. Relief valves and burst discs prevent catastrophic failure due to internal pressure buildup during vaporization.
5. Compressed Gas Cargo Tankers
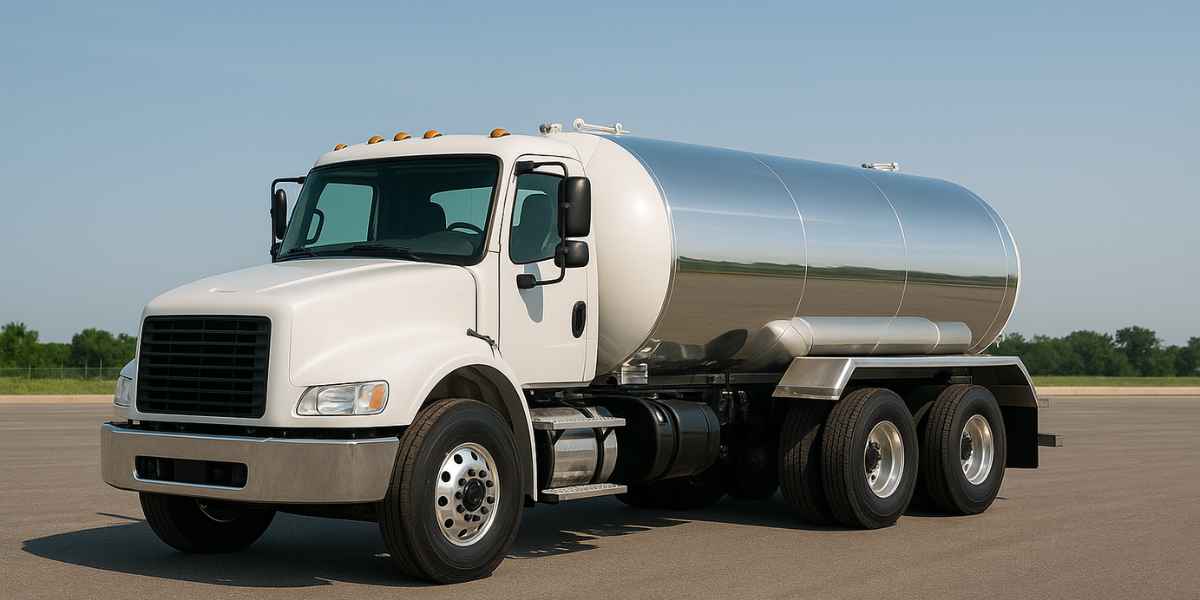
Compressed gas tankers carry gases like propane, butane, or anhydrous ammonia in liquefied or compressed form. These follow MC-331 specifications, which mandate high-strength steel tanks with spherical or cylindrical shapes for pressure equalization.
These cargo tanks include thermal protection, excess flow valves, and remote emergency shut-offs to handle volatile pressurized materials safely. Their pressure rating can reach up to 265 psi, depending on the transported gas.
6. Corrosive Cargo Tank Trucks
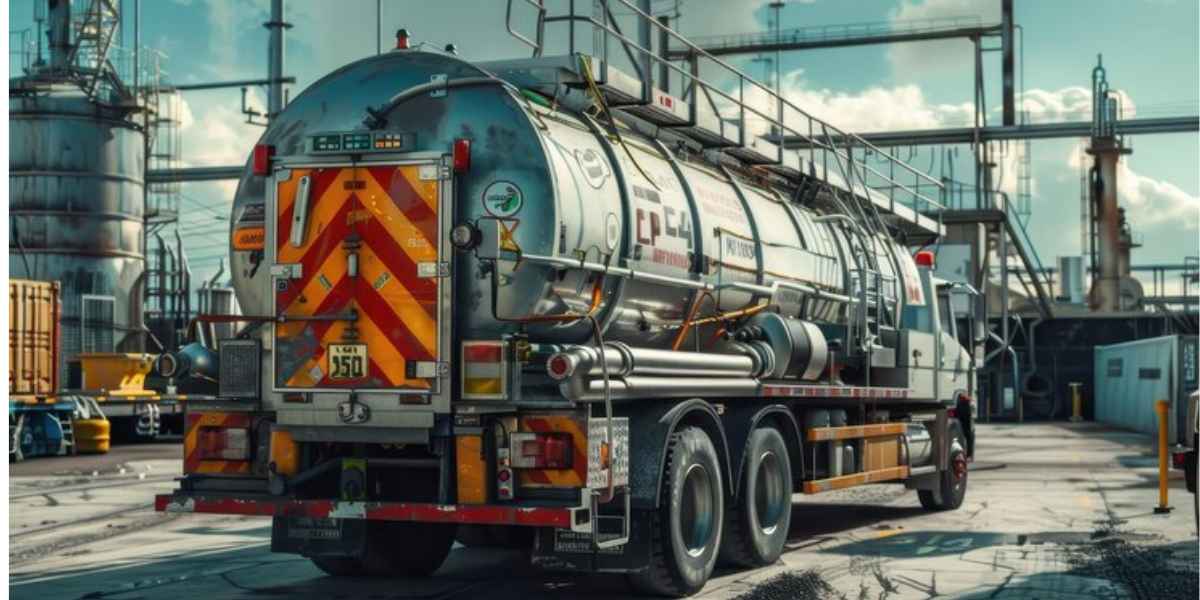
Corrosive tankers are tailored for dangerous acids like hydrochloric, sulfuric, or nitric acid. These tankers operate under DOT-412 or MC-312 standards, featuring specialized linings and gaskets to resist chemical degradation.
Their structure includes reinforced welds, PTFE gaskets, and internal coatings like rubber or epoxy. Design safeguards limit exposure and protect transport crews during loading and discharge.
Each type of tanker truck is built for specific cargo and conditions, which directly affects how much it can hold. Tank shape, wall thickness, and pressure tolerance define the safe operating capacity for every tanker configuration.
What Are the Common Capacities of Tanker Trucks?
Tanker truck capacity depends on tank design, regulatory limits, and road restrictions. Each category of tanker truck is engineered to match specific delivery needs while complying with weight distribution and cargo safety standards.
Small-Capacity Tanker Trucks
Small-capacity tanker trucks are built to carry between 3,000 and 5,000 gallons of liquid. These trucks operate on single or tandem axle configurations and are ideal for navigating tight urban roads and city-based delivery points.
They are commonly used for fuel station supply, dairy transport, or chemical delivery within metropolitan areas. Mounted on Class 7 chassis, they stay under 33,000 pounds GVWR, making them compliant with local route and bridge weight limits.
Medium-Capacity Tanker Trucks
Medium-capacity tanker trucks handle between 5,000 and 7,500 gallons of cargo. These vehicles are used for regional distribution where balance between payload and road flexibility is essential.
They often feature tandem or tri-axle designs and comply with DOT-406 or DOT-407 standards depending on whether they carry fuel, edible liquids, or regulated chemicals. Medium tankers support multi-compartment loading, which enables delivery of different products in a single run.
Large-Capacity Tanker Trucks
Large-capacity tanker trucks are designed to carry loads from 7,500 up to 11,600 gallons. These tankers dominate interstate routes, refinery-to-terminal distribution, and high-volume fuel delivery.
They use five-axle assemblies to manage bridge law compliance and are reinforced for long-distance durability. Stainless steel or aluminum tanks with multi-chamber layouts allow safe transportation of petroleum, ethanol, or liquid fertilizer over extended routes.
Specialized Cargo Tanker Trucks
Some tanker trucks are designed for lower capacities due to the nature of the cargo. Cryogenic tankers and corrosive chemical tankers typically operate with volumes between 2,000 and 5,000 gallons, not because of tank size limits but because of cargo safety requirements.
Cryogenic vessels require vacuum insulation and double-walled tanks to preserve extremely low temperatures. Corrosive tankers rely on pressure-rated linings and reduced volume to minimize risk. These specialized trucks prioritize structural containment over total load capacity.
Tanker capacity follows strict structural and legal thresholds to ensure safe material transport. These thresholds are shaped by federal safety regulations, vehicle classifications, and cargo-specific handling protocols.
Regulatory Requirements And Safety Features
Tanker trucks are required to follow DOT regulations that define their design, construction, and safe operation. Each tank type must meet specific standards such as DOT-406 for fuel or DOT-412 for corrosive liquids.
Drivers must hold a Commercial Driver’s License (CDL) with a Hazardous Materials (HazMat) endorsement to operate tankers carrying regulated cargo. This ensures they are trained in handling emergencies, loading procedures, and spill prevention.
Each tanker must pass periodic inspections that include annual visual checks and pressure tests. Trucks carrying hazardous goods must display proper placards and follow ELD mandate for tracking drive time and duty status.
What Are the Main Safety Features in Tanker Trucks?
- Pressure relief valves release excess pressure to prevent tank rupture.
- Double-walled insulation controls temperature and limits explosion risk.
- Emergency shut offs stop cargo flow during leaks or impact.
- Spill containment seals reduce fluid escape from fittings.
- Anti-surge baffles limit internal liquid movement for stability.
How Matrack Fleet Management Solutions Improves Tanker Truck Logistics?
Matrack helps tanker fleets run safer, smarter, and more efficiently by offering tools for live tracking, safety monitoring, federal compliance, maintenance alerts, and fuel management. These features work together to reduce risks, cut costs, and improve daily operations.
Real-Time GPS Fleet Tracking
Matrack GPS fleet tracking shows where every tanker is in real time. This helps dispatchers plan better routes, avoid delays, and make sure deliveries stay on schedule.
ELD Device for Federal Compliance
Matrack’s ELD device automatically logs driving hours and duty status. It keeps fleets compliant with DOT rules and removes the need for paper logs.
Driver Behavior Monitoring and Safety Alerts
Matrack tracks how each driver handles the vehicle, including speed and braking habits. The Matrack fleet dash cam adds video proof of risky behavior, making it easier to coach drivers and improve safety.
Predictive Maintenance and Vehicle Diagnostics
Matrack checks engine data and system alerts to spot issues early. This helps fleets fix problems before they turn into breakdowns or costly repairs.
Cost Control with Fleet Fuel Card
Matrack fleet fuel card tracks fuel use, controls spending, and prevents misuse. It gives fleet managers better control over fuel costs and helps manage expenses more clearly.
With these tools, Matrack makes tanker truck logistics safer, more reliable, and easier to manage day-to-day.